ENTREVISTA | TALES BRITO
“O ESPECIALISTA EM CALIBRAÇÃO”
Ana Miranda, CEO do Portal NasceCME e NasceCME Magazine, esteve na Pharma Equipamentos Peças e Serviços Ltda onde pode conversar com o sócio/diretor, Tales Brito, engenheiro e gerente técnico do laboratório de calibração. Durante o encontro, muitas questões a respeito de CME surgiram e, Ana aproveitou para preparar algumas perguntas ao “Especialista em Calibração”. Tales comenta com muito esmero, questões técnicas de extrema importância ao profissional de central de material e esterilização, tanto relacionadas a RDC n.15, quanto a diversos outros temas, como manutenção, calibração, qualificação, esterilização, indicadores biológicos, autoclave e muito mais. Com conteúdo genuíno muito aprofundado, você acompanha abaixo, a entrevista exclusiva na íntegra.
O que é qualificação? RDC n.15 estabelece:
XXII- qualificação da instalação: evidência documentada, fornecida pelo fabricante ou distribuidor, de que o equipamento foi entregue e instalado de acordo com as suas especificações.
XXIII – qualificação de operação: evidência documentada, fornecida pelo fabricante ou distribuidor, de que o equipamento, após a qualificação da instalação, opera dentro dos parâmetros originais de fabricação.
XXIV – qualificação de desempenho: evidência documentada de que o equipamento, após as qualificações de instalação e operação, apresenta desempenho consistente por no mínimo 03 ciclos sucessivos do processo, com parâmetros idênticos, utilizando-se pelo menos a carga de maior desafio, determinada pelo serviço de saúde
Qualificação é uma ação que comprova, por meio de evidências, que um equipamento foi corretamente construído, está instalado como planejado, que realiza os processos para que foi projetado e que entrega o produto de acordo com suas especificações. A comprovação que um equipamento foi corretamente construído e está instalado como o planejado, é obtida através da qualificação da instalação. A comprovação que o equipamento foi corretamente construído é obtida fazendo a comparação documentada entre a especificação e documentação técnica aprovada antes da construção com o equipamento entregue. Componentes são checados, funções são testadas, calibração é executada, dimensões verificadas e se todas estas ações comprovarem que o equipamento entregue atende as especificações de projeto e, que a documentação fornecida é aplicada ao equipamento, está garantida a correta construção do equipamento. A comprovação que o equipamento foi instalado como o planejado é obtida testando e documentando as utilidades e suas conexões. A pressão da água, pressão do ar comprimido, dimensões das tubulações, dimensões de cabos elétricos, valor da tensão de alimentação, sistema de drenagem, condições ambientais da área técnica e qualquer outra característica específica que envolve a instalação são medidas e registradas. Os valores obtidos destas medições são comparados com os requisitos solicitados pelo fabricante, que atendidos, resulta na aprovação da instalação. Então, se o equipamento foi corretamente construído, está instalado como planejado e as ações realizadas para comprovar estão documentadas, pode-se afirmar que todos os aspectos chaves da instalação física respeitam as regulamentações pertinentes e que as recomendações do fabricante foram adequadamente consideradas, ou seja, a instalação está qualificada. E como comprovar que o equipamento realiza os processos para qual foi projetado? Esta comprovação é alcançada com a aprovação dos testes da qualificação da operação ou qualificação operacional.
“E como comprovar que o equipamento realiza os processos para qual foi projetado? Esta comprovação é alcançada com a aprovação dos testes da qualificação da operação ou qualificação operacional.”
Como o assunto tratado nesta qualificação é a operacionalidade do equipamento, os testes são aplicados nos dispositivos de segurança do equipamento e no controlador do processo. Os dispositivos de segurança são desafiados por meio de simulações, como por exemplo, simular a entrada de vapor na câmara de esterilização com a porta da autoclave aberta. Desta forma todos os dispositivos de segurança são testados e os resultados dos testes documentados. A avaliação do controle é realizada em duas etapas, a primeira inclui as funções de segurança programadas no controlador e a segunda, na realização do processo em si. As funções de segurança são testadas simulando todas as falhas programadas, como o sistema de senhas para acesso a ações protegidas, que pode incluir o início de um processo de esterilização, como o acesso aos parâmetros de um ciclo de esterilização. No teste para avaliar o processo, ciclos de esterilização com a câmara sem carga são realizados, e nestes ciclos a temperatura é medida e registrada em várias posições no interior da câmara de esterilização. Também é medida e registrada o valor da pressão no interior da câmara. Com os registros das temperaturas, pressão e tempo, é possível avaliar a quantidade de ar removida da câmara na fase de remoção do ar, avaliar as temperaturas mínima e máxima, bem como a sua flutuação durante a fase de esterilização, e a pressão e temperatura na fase da secagem. Com o registro dos dados obtidos nos testes, e comparando estes dados com os critérios de aceitação preestabelecidos para os testes, é possível documentar se os critérios foram atendidos ou não. Se atendidos, pode-se afirmar que o equipamento está qualificado operacionalmente. Com a qualificação da instalação e a qualificação operacional finalizadas e aprovadas, pode-se afirmar que o equipamento está comissionado, ou seja, afirmar que o equipamento foi fornecido e instalado de acordo com suas especificações, e que está funcionando dentro dos limites predeterminados, quando operado de acordo com as instruções de operação, ou seja, o equipamento está liberado para o uso. Com o equipamento liberado para uso, a próxima etapa é avaliar se as características desejadas do produto final do processo são atendidas.

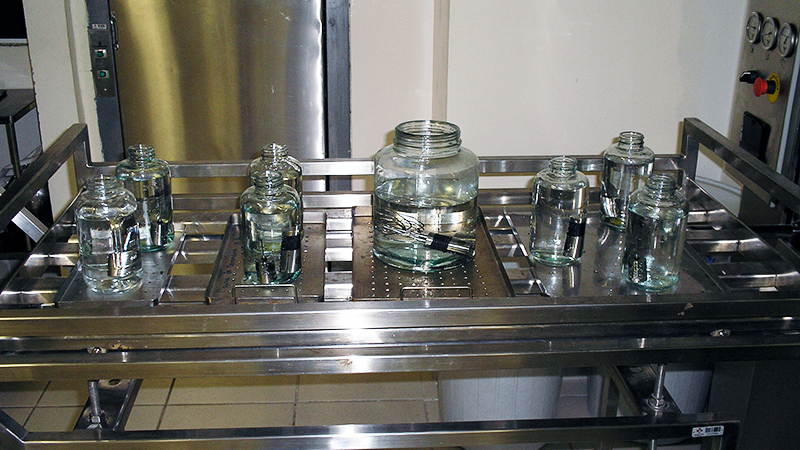
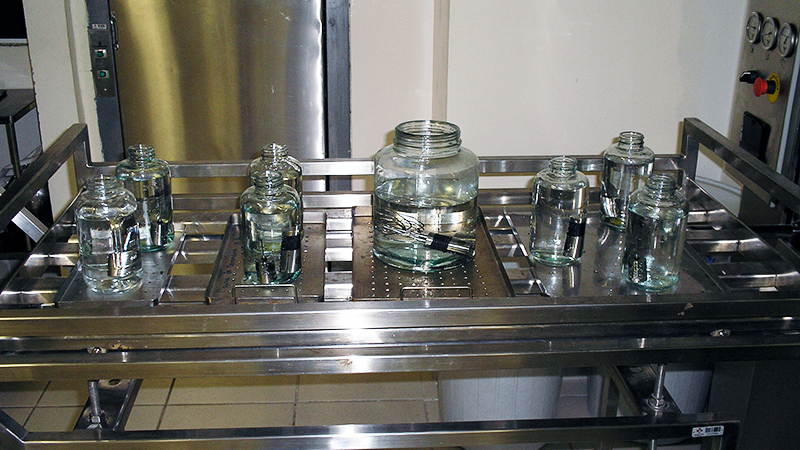


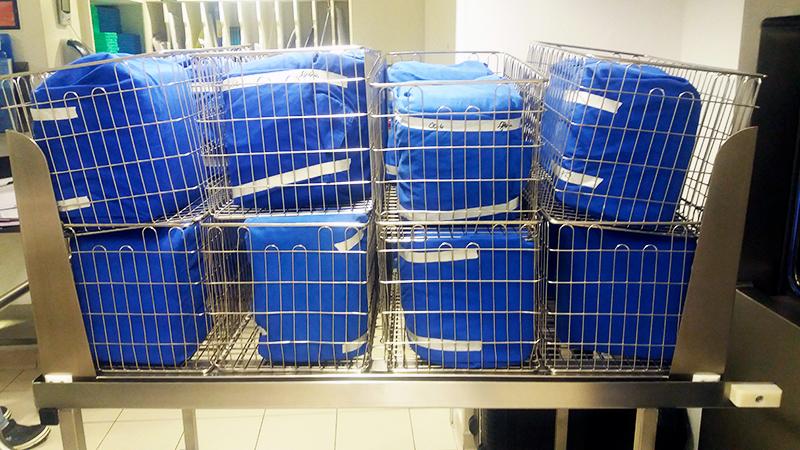
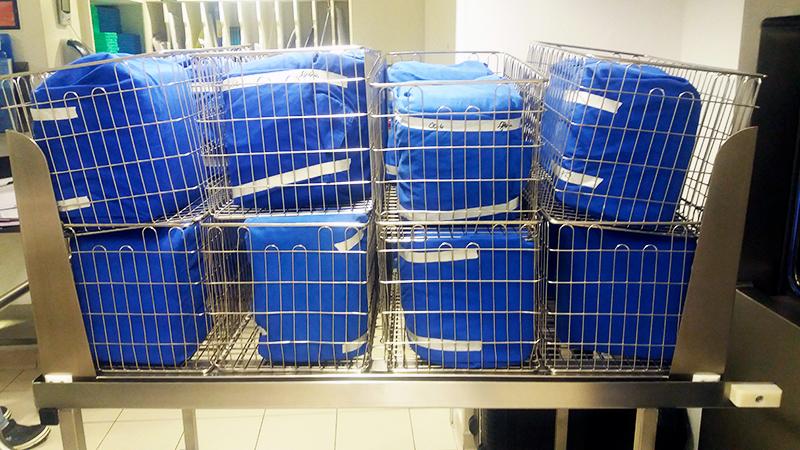
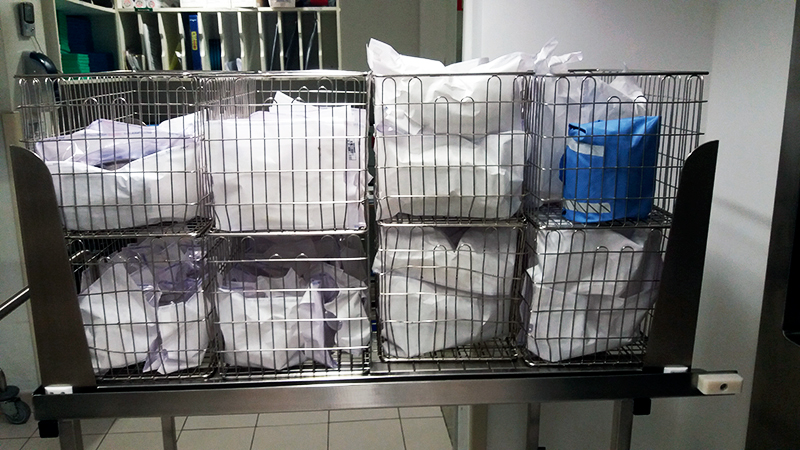
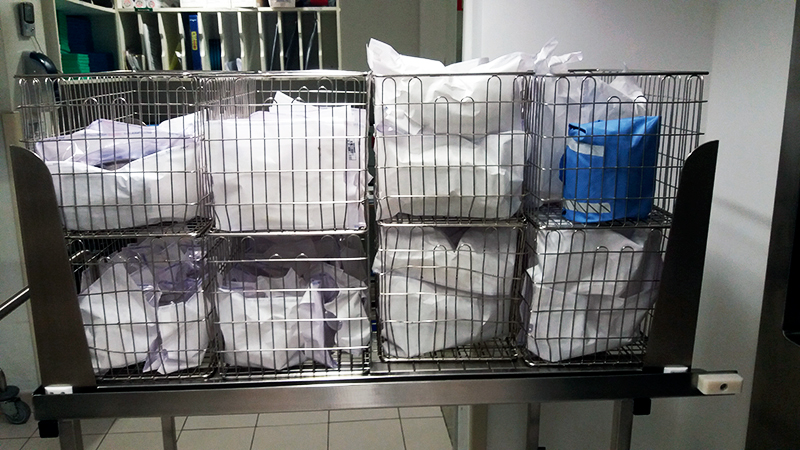


E qual é o produto produzido por um processo de esterilização?
A resposta é o material estéril.
Como avaliar a esterilidade de um material sem o mesmo perder esta característica?
Extremamente difícil, muito caro e impraticável pelo volume de material esterilizado em um hospital.
O que fazer então?
Para esse tipo de produto, somente qualificando o desempenho do processo, ou seja, a realização de ações para a obtenção e documentação de evidências de que o equipamento já comissionado produzirá produtos aceitáveis, quando operados de acordo com as instruções de operação do fabricante.
Como fazer a qualificação do desempenho do processo de esterilização?
A primeira ação é determinação da carga desafio, essa carga é obtida pelos maiores pacotes de tecidos, pelas caixas mais pesadas e pelo grau de dificuldade da penetração do vapor, como da remoção do vapor condensado. É muito importante nesse quesito solicitar do fabricante o limite de carregamento da câmara em relação ao volume e peso da carga. Uma carga pouco considerada é a carga mínima, que a grande maioria dos hospitais desconsidera. A carga mínima também deve ser qualificada, porque dependendo do tamanho da carga e dependendo também do equipamento, pode ocorrer a presença de vapor superaquecido durante a fase de esterilização do processo. Com a carga definida, é importante o posicionamento de cada item no interior da câmara. Itens que ofereçam maior dificuldade de penetração de vapor, ou de maior peso, devem ser posicionados nos pontos mais “frios” da câmara (determinados no mapeamento de temperatura com a câmara vazia da qualificação da operação), e a localização de cada item deve ser documentada. Já na carga mínima, o item a ser esterilizado deve ser posicionado no ponto mais “quente” da câmara de esterilização. Com a carga desafio estabelecida e documentada, o segundo passo é determinar o tempo de esterilização a 121,1 °C (F zero). Esse tempo deve considerar pelo menos uma redução de 12 log do microrganismo desafio para atender o método da sobremorte (over kill), que admite uma população inicial de microrganismo desafio de 106 e uma probabilidade de sobrevivência de 10-6(um em um milhão). Esse tempo nada mais é que doze vezes o valor D do microrganismo desafio a 121,1 °C (12 x D121). Com o F zero determinado, a temperatura de esterilização é fixada e o tempo de retenção calculado. Com o tempo de retenção somado ao tempo de equilíbrio chega-se ao tempo total da fase de esterilização. O tempo de equilíbrio é o tempo necessário para que a temperatura em toda a carga esteja entre as temperaturas limites da fase de esterilização, contado a partir do momento em que a temperatura de controle atinge a temperatura de esterilização. Recomenda-se a avaliação da fase de remoção de ar, e também do título do vapor (quantidade de água na fase líquida que está misturada ao vapor), que pode ser comprovada e documentada através do teste existente no mercado (teste de Bowie & Dick que avalia tanto a penetração, como o título do valor).
“Recomenda-se a avaliação da fase de remoção de ar, e também do título do vapor (quantidade de água na fase líquida que está misturada ao vapor), que pode ser comprovada e documentada através do teste existente no mercado (teste de Bowie & Dick que avalia tanto a penetração, como o título do valor).”
Finalmente a fase de secagem, que pode ser por vácuo contínuo, alto vácuo intercalado com injeção de vapor, alto vácuo intercalado com injeção de ar e o tempo de secagem. Esse tempo pode ser ajustado avaliando a massa de itens da carga antes, e no fim do processo de esterilização. A temperatura no interior da carga durante a fase de secagem pode ajudar a configurar o tempo de secagem. Com a carga desafio e os parâmetros do ciclo determinados, três processos consecutivos são realizados, medindo e registrando o tempo, a pressão na câmara de esterilização e as temperaturas nos sensores de temperatura localizados no interior da carga e ambiente da câmara. Com esses dados é possível determinar o quanto o processo foi mais ou menos letal que o projetado, e o processo será aprovado ou não. Com a aprovação do processo pode-se afirmar que o equipamento atendeu aos critérios da qualificação de desempenho. Finalizada e aprovada a qualificação de desempenho, inicia-se o processo de certificação, que é a revisão documentada de todos os resultados obtidos pelas qualificações da instalação, operacional e de desempenho, a sua aprovação é o passo final do programa de validação, permitindo assim a utilização do equipamento e a liberação do produto, ou seja: Processo de Validação: Qualificação da Instalação + Qualificação Operacional + Qualificação de Desempenho + Certificação.
A quem compete as etapas de qualificação?
Para executar as qualificações da instalação, operacional e desempenho é necessário elaborar os protocolos de qualificação.
Mas o que é um protocolo de qualificação?
O protocolo de qualificação é um plano de ação documentado, que deve ser elaborado por um profundo conhecedor do equipamento e do processo. O documento deve ser rigorosamente formatado, descrever a capacitação necessária para a execução dos testes, descrever os procedimentos de teste, possuir critérios de aceitação, conter campos para observações, aprovação/reprovação dos testes, datas, assinaturas e deve ser aprovado pelo cliente antes da implementação. Diante desta definição, com certeza, o fabricante do equipamento está naturalmente preparado para elaborar e executar os protocolos da qualificação, da instalação e operacional. Isso não quer dizer que não existam profissionais qualificados no mercado para a elaboração e execução destes protocolos, mas o conhecimento do equipamento, bem como o acesso total ao controlador do equipamento (senhas para as áreas de parâmetros e serviço), é condição fundamental para a realização desses serviços. Quanto à qualificação do desempenho, é altamente recomendável que uma empresa independente do fabricante a realize, até por questões éticas, pois a qualificação de desempenho também avalia as qualificações da instalação e de operação.
[+] Veja um exemplo de Protocolo de Qualificação da Instalação: download AQUI
A RDC n.15 Art. 37 diz que deve ser realizada qualificação de instalação, qualificação de operação e qualificação de desempenho, para os equipamentos utilizados na limpeza automatizada e na esterilização de produtos para saúde, com periodicidade mínima anual. Parágrafo único. Sempre que a carga de esterilização apresentar desafios superiores àquela utilizada na qualificação de desempenho, esta qualificação deve ser refeita. Material consignado. A quem compete o desenvolvimento dos protocolos de qualificação? Explique o parágrafo único.
Em relação à elaboração dos protocolos de qualificação a resposta anterior tratou do assunto. Na qualificação de desempenho, uma carga desafio deve ser proposta e esta carga deve ser a máxima utilizada nos processos de esterilização. Caso uma carga desafio maior for proposta, a qualificação de desempenho deve ser refeita para esta carga. Uma forma de prevenir este problema é sempre utilizar na qualificação de desempenho uma carga com desafio bem superior ao pior caso usado na rotina de esterilização. Lembrando que a carga desafio tem que respeitar os limites de ocupação da câmara recomendada pelo fabricante.
[+] Veja um exemplo de Teste da QI_verificação das Conexões das Utilidades: download AQUI
[+] Veja um exemplo de Teste QI_verificação dos Componentes Mecânicos: download AQUI
[+] Teste QO_verificação dos Alarmes: download AQUI
Que normas técnicas seguir na Qualificação do Equipamento de esterilização à vapor?
No Brasil, as normas que orientam as validações para a esterilização a vapor saturado são:
– ABNT NBR ISO 17665-1, Esterilização de produtos para saúde – Vapor. Parte 1: Requisitos para o desenvolvimento, validação e controle de rotina nos processos de esterilização de produtos para a saúde,
– ABNT NBR ISO 17665-2 – Esterilização de produtos para saúde – Vapor. Parte 2: Guia de aplicação da ABNT NBR ISO 17665-1.
Pode-se seguir orientações de outras entidades para qualificação do equipamento à vapor?
Sim, desde que as regulamentações e as normas nacionais sejam atendidas e que os testes e verificações adicionais, solicitados por estas entidades, sejam aprovados pelo proprietário do equipamento. Existem várias situações que isto acontece, principalmente na indústria farmacêutica. Empresas multinacionais que possuem fábricas instaladas em vários países, possuem normas internas, padronizadas e são elaboradas para serem aplicadas nos vários lugares onde possuem plantas. Desta forma, como o objetivo é atender as regulamentações/normalização de vários países, são normas que muitas vezes são mais rigorosas que muitas normas nacionais ou internacionais pois necessitam atender os requisitos de todos os lugares onde possuem fábricas. Diante disto, se existem outras orientações que são mais rígidas que normas nacionais, não vejo impedimento para isto, desde que as normas nacionais sejam atendidas e o proprietário do equipamento esteja de acordo.
A RDC n.15 Art. 38 diz que as leitoras de indicadores biológicos e as seladoras térmicas devem ser calibradas, no mínimo, anualmente. Comente a respeito por favor.
A calibração é um procedimento documentado que avalia o erro de indicação de grandezas físicas, e quando estes erros atingem valores limites para o processo dos equipamentos, o instrumento, se possível, deve ser ajustado. No caso da impossibilidade de ajuste, devem ser substituídos. A temperatura é uma grandeza importante para o funcionamento correto das estufas de incubação e para o processo de selagem de embalagens, para produtos estéreis e, por isto, devem ser rotineiramente calibradas. Este é um procedimento que fornece confiança ao processo, pois detecta erros na indicação da temperatura, que influenciará diretamente no controle do equipamento. Como consequência, pode ocorrer uma interpretação errada na avaliação de resultados do crescimento bacteriano na estufa, ou resultará em um produto que não atenda o objetivo do processo, como no caso de uma selagem insuficiente. Quanto ao período de calibração, a recomendação de no máximo um ano, deve inicialmente ser atendida. Mas quando o instrumento possuir um histórico de calibrações, existem ferramentas matemáticas que permitem adequar este intervalo para mais ou para menos. Mas para esta adequação é necessário a existência de um profissional que entenda de metrologia, que domine as ferramentas matemáticas disponíveis e que assuma a responsabilidade de sua decisão, e em função disto, a rotina anual pode facilitar o controle.
A RDC n.15 Art. 39 diz que a qualificação térmica e a calibração dos instrumentos de controle e medição dos equipamentos de esterilização a vapor e termodesinfecção e as requalificações de operação devem ser realizadas por laboratório capacitado, com periodicidade mínima anual. Por favor explique a qualificação térmica, calibração dos instrumentos de controle, laboratório capacitado. Comente também sobre trocar a caldeira e não esperar 1 ano para requalificar. E, comente ainda sobre o histórico das qualificações.
Da mesma forma que para as seladoras e incubadoras, as lavadoras com a função de termodesinfecção e autoclaves devem ser calibradas periodicamente e, com certeza, antes das qualificações térmicas (operação e desempenho). A calibração é um pré-requisito para as qualificações e requalificações térmicas, pois detecta desvios na indicação das grandezas (temperatura, pressão e tempo) que influenciam diretamente os resultados dos processos.
E quem pode calibrar? Quem pode qualificar?
Primeiro, é muito importante que duas empresas, independentes entre si, realizem os serviços de calibração e o de qualificação térmica. E isto porque um serviço avalia o outro. Se existe um problema, por exemplo com o padrão de temperatura utilizado por uma das empresas, isto será detectado pela outra, e a divergência vai necessitar de uma análise talvez envolvendo uma terceira empresa. A questão é quando uma empresa usa um padrão com problema, por exemplo, para calibrar os sensores de temperatura da autoclave e os sensores de temperatura do validador. Neste caso, o mesmo erro será inserido nos dois instrumentos (da autoclave e do validador), e não será detectado quando forem comparados os valores contidos no certificado de calibração e os contidos no relatório da qualificação térmica. A independência entre os serviços é uma garantia para o processo de esterilização. Vai ser mais demorado, talvez mais caro e mais trabalhoso, mas tornará mais seguro o processo de esterilização. Em relação à capacitação, empresas que prestam serviços de calibração podem ser acreditadas ou não.
E o que diferencia uma da outra?
A empresa de calibração acreditada possui implantado um sistema de qualidade, que gerencia as ações administrativas e técnicas, executadas pelo laboratório e são auditadas periodicamente (no máximo a cada dois anos) pelo CGCRE – Coordenação Geral de Acreditação, órgão do INMETRO responsável pela acreditação dos laboratórios de calibração e de ensaio. Laboratórios não acreditados ficam restritos a relações de confiança entre cliente e fornecedor, pois a capacidade de executar os serviços de calibração não passa por auditorias. No mínimo, ao escolher uma empresa de calibração, deve-se exigir que os padrões utilizados nas calibrações sejam calibrados em laboratórios acreditados (calibração rastreada). Quanto às qualificações, as empresas prestadoras deste serviço também podem ser acreditadas para ensaios e isto, como na calibração, é uma garantia de que os serviços executados atendem um sistema de qualidade que minimizam erros e a capacitação da empresa passa por auditorias periódicas. Hoje, pouquíssimas empresas de validação possuem a acreditação, mas conheço algumas com o sistema de qualidade implantado e em processo de acreditação. Com certeza em breve isto será um divisor entre as empresas prestadoras deste serviço.
Mas o que exigir de uma empresa de qualificação térmica?
Primeiro é o domínio da teoria da desinfecção e esterilização, o conhecimento profundo dos equipamentos (termodesinfectoras e autoclaves), domínio da metrologia, conhecimento das resoluções e normas aplicadas no serviço e responsabilidade técnica. Outro item importante é a qualidade dos equipamentos utilizados na aquisição das grandezas temperatura, pressão e tempo. Com raras exceções, os sensores de temperatura existentes nas termonfectoras e nas autoclaves são superiores em qualidade, quando comparados aos termopares utilizados pelos validadores e, por isto, a qualidade do validador como a do termopar tem papel fundamental nos resultados do serviço. E por esta diferença de qualidade, a verificação e documentação das indicações dos sensores de temperatura e do sensor de pressão do validador devem ser checados antes e depois da realização das qualificações, de maneira a garantir que os valores registrados pelos validadores estejam dentro de erros aceitáveis. E lógico, o histórico dos serviços de qualificação também é uma forma de avaliar a qualidade dos serviços prestados pela empresa.
Você considera que há necessidade da periodicidade mínima anual? Essa recomendação atende aos padrões de equipamentos comercializados apenas no Brasil, ou atende padrão de recomendação internacional?
A rotina de calibração/qualificação anual é uma recomendação internacional. Em alguns casos a rotina tem períodos menores que o anual. Os sistemas de qualidade minimizam erros, mas por outro lado desprezam a capacidade técnica dos profissionais. Vou tentar explicar: nos processos de esterilização, principalmente nas CMEs, existem e são aplicados vários procedimentos para garantir que o processo está adequado. Como primeiro exemplo, posso citar o teste de Bowie & Dick. Este teste é realizado diariamente, em todas as autoclaves, na grande maioria dos CMEs existentes no pais. Com este teste fica comprovado que em 3,5 minutos (alguns fabricantes comprovam que em um minuto) o vapor penetra no pacote teste. E o que pode se concluir disto? Que a fase de remoção de ar executada pela autoclave atende o especificado. Segundo exemplo: Muitas centrais de esterilização utilizam o Indicador Biológico (IB) rotineiramente em seus processos de esterilização. O que isto demonstra? Que o desempenho do equipamento está mantido. Principalmente quando testes específicos com a metade do tempo de esterilização são executados e aprovados. Terceiro exemplo: Os indicadores ou integradores químicos que são utilizados em todos os processos de esterilização fornecem evidências que presença de vapor, temperatura e tempo de exposição são atendidos. E mais ainda, todas as rotinas de manutenção preventiva foram realizadas, documentadas e nenhum problema grave encontrado, inclusive a calibração dos instrumentos de medição instalados na autoclave, comprovando que temperatura, pressão e tempo estão dentro dos limites de erros aceitáveis. Se em uma autoclave, durante o ano todo, todos estes testes foram aprovados e documentados não haveria a necessidade de uma requalificação obrigatória depois de exatamente um ano da qualificação já executada.
“É lógico que as qualificações térmicas do processo de esterilização é mais uma garantia para o processo, mas o período entre qualificações deveria ser atribuído ao proprietário da autoclave e claro, desde que demonstre por meio de evidências os resultados das avaliações e intervenções rotineiras e que assuma a responsabilidade.”
É lógico que as qualificações térmicas do processo de esterilização é mais uma garantia para o processo, mas o período entre qualificações deveria ser atribuído ao proprietário da autoclave e claro, desde que demonstre por meio de evidências os resultados das avaliações e intervenções rotineiras e que assuma a responsabilidade. Por outro lado, se na rotina de avaliações forem encontrados problemas recorrentes, tanto a calibração como a requalificação térmica podem ser necessárias antes do período de um ano.
[+] Veja um exemplo de Rotina de Manutenção em Autoclave: download AQUI
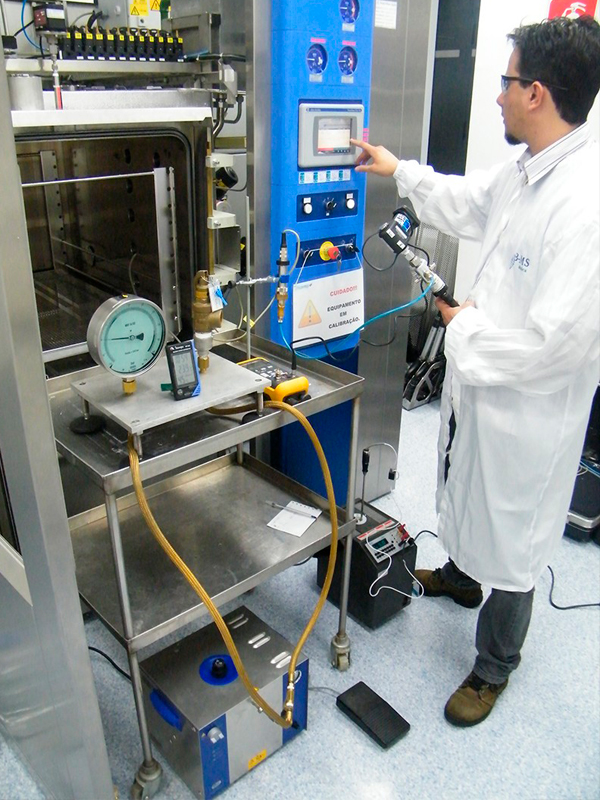
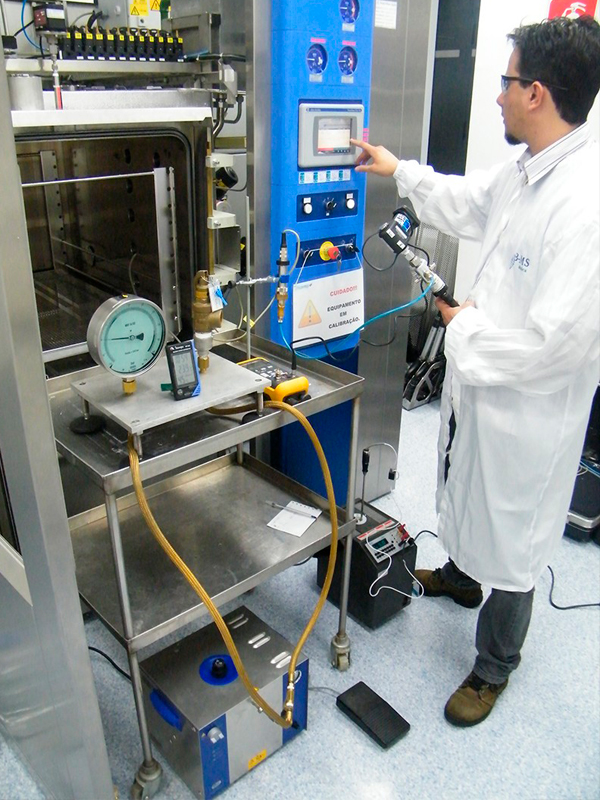
A RDC n.15 Art. 40 diz que na manutenção dos equipamentos, as informações resultantes das intervenções técnicas realizadas devem ser arquivadas para cada equipamento, contendo, no mínimo:
I – Data da intervenção;
II – Identificação do equipamento;
III – Local de instalação;
IV – Descrição do problema detectado e nome do responsável pela identificação do problema;
V – Descrição do serviço realizado, incluindo informações sobre as peças trocadas;
VI – Resultados da avaliação dos parâmetros físicos realizados após a intervenção e complementados com indicadores químicos e biológicos, quando indicado;
VII – Nome do profissional que acompanhou a intervenção e do técnico que executou o procedimento.
Parágrafo único. O prazo de arquivamento para o registro histórico dos equipamentos de saúde deve ser contado a partir da desativação ou transferência definitiva do equipamento de saúde do serviço. No descritivo deste artigo poderia ser acrescentado número de lote ou número de série das peças de reposição? Cite quais?
Sim, mas nem todos os componentes da autoclave possuem números de série. Bomba d’água, bomba de vácuo, transmissores de pressão, alguns sensores de temperatura, e outros componentes de uma autoclave possuem número de série, mas a grande maioria dos componentes não. Por isto, a importância do departamento de engenharia no hospital. Felizmente a engenharia clínica e hospitalar é uma realidade em grande parte dos hospitais no Brasil, e os serviços de manutenção realizados por terceiros, com contrato ou não, devem ser acompanhados por técnicos destes departamentos, com a capacidade não só de avaliar o problema em um componente da autoclave que necessita de substituição, mas também a influência do componente no processo realizado pelo equipamento. Se a chave elétrica que liga/desliga as resistências do gerador de vapor, denominada de contatora, está danificada e no final de sua vida útil, necessita de ser substituída. A substituição é realizada por outra contatora com a mesma especificação (sendo do mesmo fabricante ou não), e o sistema de aquecimento do gerador de vapor volta a funcionar como antes. Neste caso nenhuma ação a mais é necessária, e o processo executado pela autoclave está garantido. Por outro lado, se o sensor de temperatura do dreno do equipamento está danificado e necessita de ser substituído. Neste caso não basta apenas substituir e verificar se a temperatura voltou a ser a indicada. É necessário que pelo menos uma verificação da indicação da temperatura seja realizada e comparada com a indicação de um padrão e se necessário, o ajuste seja realizado.
“É necessário que pelo menos uma verificação da indicação da temperatura seja realizada e comparada com a indicação de um padrão e se necessário, o ajuste seja realizado.”
Após confirmar que a indicação da temperatura esteja dentro da especificação do equipamento, o instrumento deve ser calibrado para documentar e evidenciar que os erros encontrados estão dentro do critério estabelecidos para o equipamento. Com estas ações pode-se dizer que o processo executado pela autoclave está garantido.
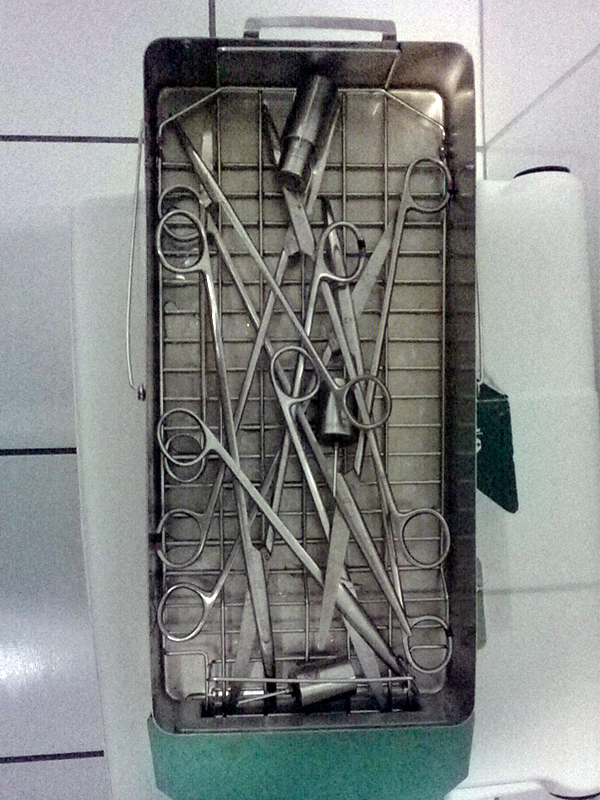
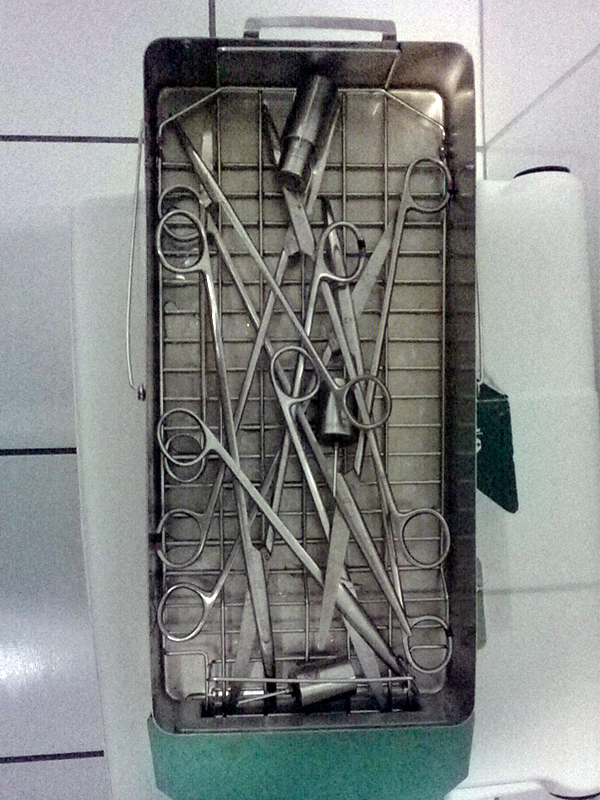
A RDC n.15 Art. 41 diz que todos os equipamentos de limpeza automatizada e esterilização devem ter seu processo requalificado após mudança de local de instalação, mau funcionamento, reparos em partes do equipamento ou suspeita de falhas no processo de esterilização. Parágrafo único. Na requalificação dos equipamentos de esterilização deve-se incluir o uso de indicadores biológicos e químicos. Requalificação: a) após mudança de local de instalação; b) mau funcionamento; c) reparos em parte do equipamento ou suspeita de falhas de esterilização. Quando um equipamento muda seu local de instalação, deve ser novamente validado, ou seja, executar os protocolos das qualificações da instalação, da operação e de desempenho. Comente a respeito.
A questão é verificar se todo o protocolo necessita ser refeito. Por exemplo, uma autoclave foi transportada sem ter as partes críticas desmontadas (tubulações, componentes, controlador, etc.), a qualificação da instalação pode ser resumida aos testes relacionados às utilidades, ambiente e funcionamento dos componentes do equipamento. Neste caso ainda, a qualificação da operação se resumiria aos testes dos dispositivos de segurança e ao mapeamento térmico com a câmara vazia, e a qualificação de desempenho deveria ser refeita na sua totalidade. Agora, em relação a mau funcionamento, reparos ou suspeita de falhas de esterilização, uma avaliação deve ser feita para detectar o motivo do mau funcionamento, do reparo ou da falha na esterilização. Exemplificando, o equipamento sofreu um mau funcionamento porque a válvula de injeção de vapor danificou e o vapor continuou entrando na câmara mesmo com a válvula fechada. O processo sofreu uma falha por temperatura alta na fase de esterilização. Com o problema detectado e a válvula substituída, não teria o porquê da requalificação. Apenas a documentação da ação da manutenção basta para evidenciar que o motivo do mau funcionamento foi resolvido, e o equipamento voltou ao seu estado de operacionalidade. Um caso mais grave, ocorre uma falha no processo, durante a fase de esterilização e foi detectado que o sensor responsável pelo controle da temperatura na câmara de esterilização está quebrado e o processo é interrompido e finalizado pela engenharia do hospital.
Neste caso, o que fazer?
Não tem jeito, o sensor de temperatura tem que ser substituído. E além da substituição, a indicação de temperatura deverá ser comparada com a indicação de um sensor de temperatura padrão e do resultado desta comparação o ajuste da indicação pode ser necessário ou não.
Mas o que é importante?
A comparação entre os resultados obtidos na verificação do sensor com o padrão (com ajuste ou não) deve ser comparada com os resultados informados no certificado da calibração realizadas antes da última qualificação. Se os resultados forem compatíveis, ou seja, a informação que o controlador recebe do sensor mantém as condições anteriores à substituição, entendo que a requalificação não é necessária. Por outro lado, se o controlador da autoclave foi substituído por outro modelo, ou o software foi alterado, ou a substituição de componentes que influenciam diretamente o processo, que possuam características diferentes dos originais são motivos para a avaliação do impacto, para se determinar quais são os testes necessários para garantir que o equipamento volte a ter o desempenho necessário. Resumindo, mau funcionamento, reparos e falhas devem ser avaliados para se determinar qual o impacto no processo e determinar as ações necessárias, inclusive a necessidade de requalificação. Uma observação final, o texto da RDC deveria ser mais específico.
Qual a quantidade mínima de indicador químico e indicador biológico em função do tamanho da câmara do esterilizador? Existe alguma norma técnica que estabelece orientação a respeito?
Este é um assunto que não domino muito, mas entendo que os indicadores/integradores químicos devem ser utilizados para a liberação do produto estéril no momento do uso. Desta forma deveriam estar em todos os pacotes e caixas de instrumental esterilizados ou pelo menos nos itens críticos das cargas esterilizadas. Em relação aos indicadores biológicos, vou colocar minha opinião. Eles até podem ser utilizados como liberadores de carga e neste caso, deveria ser colocado em um pacote desafio e estes pacote posicionado na carga de modo que fique na região de menor temperatura na câmara, região determinada durante a qualificação de operação. Isto na rotina diária da esterilização. Outra forma de usar os indicadores biológicos é fazer uma carga padronizada, composta apenas de pacotes desafios com um indicador biológico em cada pacote. Esta carga seria esterilizada em um ciclo especial, com todos os parâmetros do ciclo normal, mas com a metade do tempo de esterilização (ou com o tempo proporcional à carga microbiana do IB, por exemplo se carga do IB é na ordem de 105, o tempo de esterilização deveria ser de 5/12 do tempo validado). Este ciclo seria executado periodicamente e não poderia haver crescimento em nenhum dos indicadores biológicos utilizados. Este procedimento seria uma forma de confirmar a qualificação de desempenho, ou seja, confirmar que o processo usado na rotina diária da esterilização atende as 12 reduções logarítmicas da bactéria desafio para o agente esterilizante utilizado.
A RDC n.15 Art. 93 diz que é obrigatório a realização de teste para avaliar o desempenho do sistema de remoção de ar (Bowie & Dick) da autoclave assistida por bomba de vácuo, no primeiro ciclo do dia. Teste de B&D (Bowie & Dick) no primeiro ciclo do dia? Esse enunciado não está equivocado?
Realizar teste de Bowie&Dick no primeiro ciclo do dia é uma citação que ouço há mais de 20 anos. Sempre entendi que o teste deveria ser realizado partindo da autoclave fria, apesar de existir fabricantes que recomendam um ciclo de aquecimento antes da realização do teste. E também temos que considerar que grande parte das CMEs trabalham 24 horas por dia e o tempo necessário para esfriar uma autoclave é enorme e que, nestes casos, parar o equipamento não é interessante para o processo produtivo da CME. O teste é importante, não avalia apenas o funcionamento da bomba de vácuo, mas também vazamentos ou presença de gases não condensáveis no vapor. E existem testes que permitem avaliar inclusive o título do vapor. Em relação a frequência, a questão é, ocorreu uma falha no teste, o que fazer com as cargas produzidas na autoclave desde a realização do teste anterior? Tem lugar que itens destas cargas já foram utilizados, mas o ideal seria condenar todos os itens esterilizados no período entre testes. Se for possível armazenar todo o material esterilizado em um determinado período, e só ser liberado após a realização do teste seguinte, o período entre testes pode ser igual ao da possibilidade de manter o material armazenado. Como na maioria das vezes isto não é aplicável, a rotina diária é uma boa ideia e pode ser realizado a qualquer hora do dia, desde de que repetido o horário todos os dias.
“Como na maioria das vezes isto não é aplicável, a rotina diária é uma boa ideia e pode ser realizado a qualquer hora do dia, desde de que repetido o horário todos os dias.”
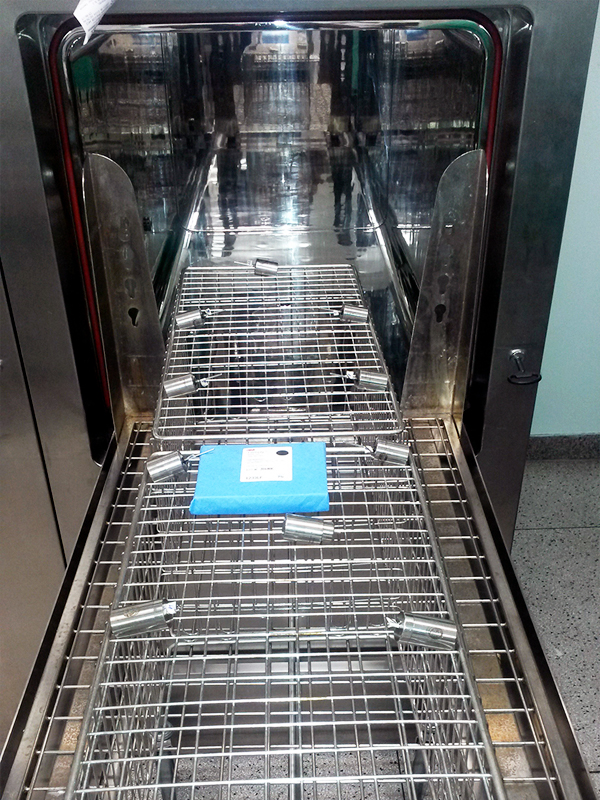
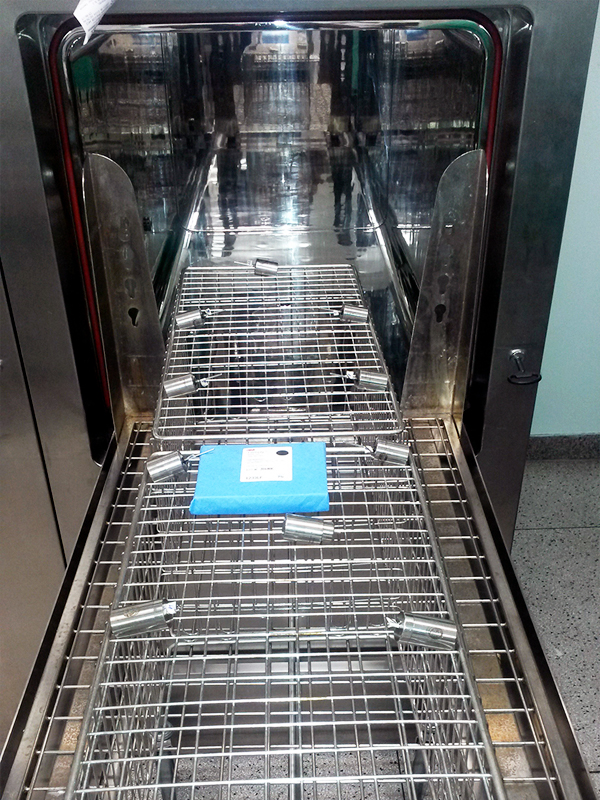
A RDC n° 15 Art. 94 diz que não é permitido a alteração dos parâmetros estabelecidos na qualificação de operação e de desempenho de qualquer ciclo dos equipamentos de esterilização. Você poderia exemplificar a situação?
Eu tenho um entendimento diferente em relação à qualificação operacional citada no art. 94 da RDC 15. Primeiro, os ciclos executados na qualificação operacional têm objetivo diferente dos ciclos executados na qualificação de desempenho. Na qualificação operacional, um dos objetivos é avaliar o controle do equipamento na execução do processo. Por isto o tempo ajustado para a fase de esterilização deve ser aquele que permitirá avaliar o perfil da temperatura no interior da câmara de esterilização vazia, os limites permitidos como a sua uniformidade no decorrer do tempo. Quanto maior o tempo, melhor será o resultado da avaliação. Trabalho para um fabricante de autoclaves que recomenda que o tempo de esterilização para os ciclos executados na qualificação operacional seja igual a 20 minutos e tem ciclo qualificado no desempenho com tempo de esterilização de 4,5 minutos para a temperatura de 135 °C. Assim, o tempo de esterilização do ciclo executado na qualificação operacional pode, e na maioria das vezes é, diferente do tempo de esterilização dos ciclos avaliados durante a qualificação de desempenho. Em relação aos parâmetros dos ciclos aprovados na qualificação de desempenho concordo com a manutenção dos parâmetros das fases de remoção de ar e de esterilização, mas alterações no tempo ou no modo de secagem não tem influência na letalidade do ciclo.
No Art. 95, a água utilizada no processo de geração do vapor das autoclaves deve atender às especificações do fabricante da autoclave. Isto significa que fica estabelecido que o fabricante determina as especificações da água utilizada no processo de geração do vapor das autoclaves. Ou seja, se a CME tiver 3 (três) autoclaves de marcas diferentes e os três fabricantes adotarem especificações de água diferentes, o serviço de esterilização deverá atender as especificações individuais das as empresas? Isto é factível na prática?
A qualidade da água para a geração de vapor utilizado em autoclaves hospitalares é recomendada em normas e a indicação do fabricante deve pelo menos atender estas recomendações. Um exemplo é dado abaixo:
Tabela 1: Contaminantes da água de alimentação para gerador de vapor dedicado.
Identificação | Água de alimentação |
Resíduos na evaporação | ≤ 10 mg/l |
Silicatos (SiO2) | ≤ 1 mg/l |
Ferro | ≤ 0,2 mg/l |
Cadmio | ≤ 0,005 mg/l |
Chumbo | ≤ 0,05 mg/l |
Resíduos de metais pesados exceto o ferro, cadmio e chumbo | ≤ 0,1 mg/l |
Cloretos (Cl) | ≤ 2 mg/l |
Fosfato (P2O5) | ≤ 0,5 mg/l |
Condutividade (em 25 °C) | ≤ 5 µS/cm |
Valor do pH (grau de acidez) | ≤ 5 a 7,5 |
Aparência | Incolor, limpa e sem sedimentos |
Dureza | ≤≤ |
Nota: A conformidade deverá ser testada de acordo com método analítico reconhecido |
A tabela acima foi retirada do anexo B (informativo) da norma europeia EN 285 e aplicada para a água de alimentação do gerador de vapor acoplado as autoclaves. Esta norma também recomenda limites de contaminantes para o vapor de alimentação, quando gerado a partir de gerador central. Por outro lado, existem processos que exigem água com limites de contaminantes mais rígidos, com em muitas aplicações na indústria farmacêutica, onde o termo vapor puro, com especificação de limites de contaminantes própria, é muito utilizado. E nestes casos, na maioria das vezes, a autoclave é construída especificamente para o processo e possui exigência mais rígidas das aquelas utilizado em CMEs.
Qual o perfil técnico do engenheiro que realiza qualificação de equipamento à vapor?
O profissional que executa a qualificação tem que conhecer a teoria dos processos de esterilização, tem que conhecer o funcionamento dos componentes que compões uma autoclave, conhecimentos de instrumentação e controle, dominar a leitura de esquemas mecânicos e elétricos, conhecimentos da termodinâmica, principalmente a do vapor d’água, noções de procedimentos de qualidade e conhecimentos de metrologia. É uma área multiprofissional e não necessita ser necessariamente um engenheiro. Pode ser tecnólogos ou técnico e não importa muito de qual área veio (mecânica, elétrica, química, farmacêutica etc.), vai ter a necessidade de adequar seus conhecimentos às exigências do serviço.
Esse mesmo engenheiro tem competência para realizar a qualificação de tecnologias à baixa temperatura?
Sim, desde que domine a tecnologia do equipamento. O comissionamento ou a qualificação da instalação e operacional é aplicada à grande maioria dos equipamentos. Qualquer equipamento que execute uma função em um processo produtivo tem que ser instalado e testado. Mas quem cria e/ou executa um protocolo de qualificação tem que ter domínio da tecnologia empregada e, na área de esterilização, da teoria de esterilização.
Que norma técnica deve ser seguida na qualificação das tecnologias à baixa temperatura? 18.1 Formaldeido?
Não conheço norma especifica para a validação de processo de esterilização utilizando a formaldeído como agente esterilizante. Mas a norma ABNT NBR 15659: Esterilização de produtos para saúde ´Esterilizadores de vapor a baixa temperatura e formaldeído – Requisitos e métodos de ensaio, que apesar de ser uma norma aplicada à construção de esterilizadores fornece subsídios para a validação do equipamento.
18.2 Óxido de etileno
Sim, existe uma norma específica para a validação de esterilizadores por óxido de etileno, a ABNT NBR 15245: Produtos para saúde ´Validação e controle da rotina da esterilização por óxido de etileno.
18.3 Peróxido hidrogênio (vaporizado, gasoso)
Não conheço normas específicas para processos de esterilização utilizando o peróxido de hidrogênio como agente esterilizante, mas nestes processos que usam agentes físicos (temperatura) e agentes químicos a temperatura tem que ser mapeada, a presença do agente químico confirmada e na qualificação de desempenho a bactéria desafio ao processo deve ser usada como condição essencial para a aprovação do processo. Realçando novamente, o ideal seria usar um indicador biológico com carga microbiana de 1012 para a garantia de doze reduções logarítmicas. Como este Indicador Biológico não é fácil de se encontrar no Brasil, é recomendado alterar o tempo de exposição pela metade se for usado um IB com carga de 106ou um tempo proporcional em função da carga do IB.
O que é imprescindível que o enfermeiro exija da empresa que presta serviço de qualificação de equipamentos? Comente sobre o manual do serviço antes da compra detalhado com senhas de serviço.
Vou dividir o assunto em duas partes, a validação de um equipamento novo e em requalificações. Equipamento novo a qualificação deve ser iniciada antes da compra. E o porquê? Se existe um protocolo descrevendo os procedimentos para ser aplicado no processo de compra, a comparação entre fornecedores se torna mais fácil e a aquisição mais segura. Neste procedimento, devem ser considerados itens como:
– Pessoal envolvido e suas atribuições. Neste item ficam especificados a quem atribuir a especificação do equipamento, quem será o responsável pelo contato com os fornecedores, quem participará do processo decisório.
– Especificação: Não basta mais falar que precisa de uma autoclave de 500 litros. A especificação, além do volume deve conter uma especificação mais precisa do equipamento como material utilizado, procedimentos de soldas utilizadas, especificação precisa do controlador, treinamento de operação, treinamento para equipe de manutenção do hospital, qualidade dos componentes, reposição de peças, garantia, peso do equipamento, área ocupada pelo equipamento, descrição dos processos de esterilização desejados, a documentação fornecida (manuais de instalação, operação e manutenção incluindo a especificação de cada componentes utilizado na autoclave), especificação das utilidades disponíveis, senhas de acesso (operação, parâmetros, serviço e programação), condições ambientais, emissão de calor para o ambiente, emissão de ruído, funções de segurança desejadas, sensores de temperatura e pressão, linguagem aplicada no controlador, assistência técnica (disponibilidade para o local e tempo de resposta), e outras necessidade específicas para o hospital como lista de clientes da empresa fornecedora, fornecimento de protocolos e serviços de comissionamento, número de equipamentos instalados no pais, tempo de operação no pais no caso de equipamentos importados (isto é importante pois empresas de nome já entraram no pais, venderam alguns equipamentos e saíram do pais deixando clientes sem o suporte necessário e muitas vezes dependendo de importação de peças e até de serviços), tempo para o fornecimento do equipamento, tempo necessário para a instalação, rotas e dimensões de acesso para o local da instalação, etc.
– Critérios de aceitação: idoneidade da empresa, diferenciação por meio de pontuação ou classificação (não crítico, semicrítico, crítico, indispensável) de cada item da especificação, critérios para desempate, preço, condições de pagamento, tempo de fornecimento, tempo para o transporte e instalação e comissionamento.
– Renegociação
– Contrato de compra
Depois de executado o procedimento de compra, que pronto pode ser aplicado para outros equipamentos, a aquisição, a instalação e o comissionamento do equipamento fica resolvido. A próxima etapa é a contratação da qualificação de desempenho que será tratada na requalificação. Os requisitos necessários para a compra da requalificação, ou seja, o mapeamento dos ciclos com câmara vazia como parte da qualificação de operação e qualificação de desempenho serão tratados agora. A primeira etapa para a requalificação de uma autoclave é a calibração de seus instrumentos e preferencialmente deve ser uma empresa diferente daquela que irá executar a qualificação de desempenho. E a contratação de uma empresa de calibração tem alguns requisitos, e entendo que o primeiro deles é dar preferência para uma empresa acreditada. Empresas não acreditadas pelo CGCRE do INMETRO, não são auditadas periodicamente e por isto a única garantia que o contratante pode ter é a relação de confiança que possui com a empresa de calibração. Se você conhece a capacidade técnica e o comportamento ético da empresa e aprova, não tem porque não contratá-la.
“Empresas não acreditadas pelo CGCRE do INMETRO, não são auditadas periodicamente e por isto a única garantia que o contratante pode ter é a relação de confiança que possui com a empresa de calibração. Se você conhece a capacidade técnica e o comportamento ético da empresa e aprova, não tem porque não contratá-la. “
Outra coisa importante a ser levada em conta de uma empresa de calibração é sua CMC, capacidade de medição e calibração. Isto indica o erro que os instrumentos usados na calibração possuem. Por exemplo, sua autoclave lê temperatura com uma casa depois da vírgula e a CMC da empresa de calibração é 0,25 °C. Esta empresa, se se contratada, vai usar instrumentos padrão que tem erro maior do que dos instrumentos da autoclave e isto é inconsistente. O padrão utilizado deve possuir qualidade de medição melhor do instrumento que será calibrado e questionamento sobre a CMC do laboratório é um fator crítico para a sua contratação. Com toda instrumentação relacionada a medição e proteção do equipamento calibrada e com os resultados aprovados, a autoclave está pronta para ser requalificada e a requalificação da operação pode ser iniciada. A qualificação operacional é um procedimento simples pois seus critérios de aceitação são fáceis de avaliar. A temperatura mínima na fase de esterilização deve ser maior ou igual à temperatura de esterilização, a máxima igual a temperatura de esterilização mais 3 °C, cada sensor de temperatura não pode indicar variação de temperatura maior do que ±1 °C e a diferença entre qualquer sensor não pode ser maior que 2 °C e a pressão durante toda a fase deve ser compatível com a temperatura para avaliar se o vapor atende a condição de saturado. Qualquer empresa com um bom sistema de aquisição e registro de temperatura, pressão e tempo está apta para realizar este serviço. Mas na qualificação de desempenho é diferente. Determinação e/ou avaliação da carga desafio, posicionamento dos itens na carga, especificação da letalidade mínima, determinação das pressões mínimas e máxima na fase de remoção de ar, avaliação do tempo de penetração do vapor na carga (tempo de equilíbrio), tempo de exposição (tempo de retenção), tempo de secagem e avaliação do desempenho da secagem, análise da qualidade do vapor saturado, etc. são conhecimentos que o fornecedor deste serviço deve dominar para que depois das coletas de dados tenha a condição de executar a certificação das qualificações e a sua aprovação para considerar o equipamento requalificado. Além do domínio do conhecimento, o equipamento utilizado para a aquisição de dados deve ter qualidade suficiente para atender os requisitos do serviço. Existem equipamentos que trabalham com erros de 0,5 °C e estes não podem ser usados. Marcas como Ellab, Kaye, Yokogua, Keysight (ex Agilent), Fluke, Eurotherm, etc fabricam equipamentos confiáveis e podem ser usados nos serviços. Então o equipamento atende, mas e os cálculos realizados para a letalidade? É um software especifico do equipamento ou os cálculos são realizadas por planilhas próprias das empresas de qualificação? Estas planilhas foram validade? Os sistemas de coletas de dados são ajustados e verificados antes e depois das realizações do serviço? E os padrões utilizados para a verificação da temperatura, pressão e tempo, foram calibrados em laboratórios da Rede Brasileira de Calibração? A empresa é acreditada pelo CGCRE do INMETRO? Resumindo, os equipamentos e procedimentos do ensaio possuem a qualidade necessária para a garantia dos resultados? Muito importante é o histórico da empresa: tempo de atuação no mercado, carteira de clientes, modelo de relatório, atendimento de cronograma, e a pesquisa de satisfação com outros clientes que usaram o mesmo serviço e, finalmente o preço, que deve ser compatível com o trabalho realizado.
“Muito importante é o histórico da empresa: tempo de atuação no mercado, carteira de clientes, modelo de relatório, atendimento de cronograma, e a pesquisa de satisfação com outros clientes que usaram o mesmo serviço e, finalmente o preço, que deve ser compatível com o trabalho realizado.”
Você poderia descrever sucintamente a finalidade desses componentes da autoclave, por favor, e também estimar a vida útil?
21.1 válvula redutora
Autoclaves usam válvulas redutoras de pressão para ar comprimido e para o vapor, quando a autoclave é alimentada por uma central de geração de vapor. Sua função é a de reduzir e limitar a pressão. A válvula redutora simples age apenas como limitadora de pressão e quando utilizada próximo ao limite da sua vazão não consegue manter a pressão de saída no valor de ajuste. Por este motivo, quando aplicadas na alimentação de vapor centralizada, a melhor opção é a válvula redutora auto operada, que consegue controlar a pressão de saída mesmo com a variação no consumo do vapor. Estas válvulas possuem pouca manutenção e a vida útil é muito grande, podendo falar em décadas.
21.2 bomba de vácuo
Componente que tem grande importância no funcionamento do processo. É responsável pela remoção de ar da câmara de esterilização e carga e com isto permitindo a penetração do agente esterilizante. Também importante no processo de secagem da umidade presente na carga, principalmente nas autoclaves que utilizam vapor de água pura ou em misturas com outros agentes esterilizantes. Existem vários tipos de bomba de vácuo, mas devido ao vapor as mais utilizadas são as de anel líquido. O funcionamento da bomba de vácuo de anel líquido pode ser visualizado no link: [+] http://www.gdnash.com.br/funciona.html. As bombas de vácuo de anel líquido são máquinas rotativas e não existe contato entre partes metálicas no seu interior, possuem alta profundidade de vácuo, baixa manutenção e grande durabilidade. Possui dois inconvenientes, o primeiro é a cavitação, que são pequenas implosões de bolhas de vapor no seu interior que podem danificar a parte interna da carcaça do rotor e o consumo de água potável. Tanto a cavitação como o consumo de água podem ser regulando a vazão de água para o anel líquido e a vazão de ar para minimizar os efeitos da cavitação. O consumo de água também pode ser minimizado usando a circulação da água descartada pela bomba (tecnologia usada por alguns fabricantes) ou o uso de um tanque para resfriamento e reutilização da água para a geração do anel líquido. Também estão utilizando bombas de vácuo de palhetas, com consumo zero de água, mas com contato entre as palhetas e a parte interna da carcaça do rotor, o que vai gerar a necessidade maior de manutenção. Como este tipo de bomba tem aplicação recente em autoclaves, dados de manutenção ficam prejudicados. Independente do tipo de bomba utilizada, é um componente fundamental para o funcionamento da autoclave.
“O consumo de água também pode ser minimizado usando a circulação da água descartada pela bomba (tecnologia usada por alguns fabricantes) ou o uso de um tanque para resfriamento e reutilização da água para a geração do anel líquido. Também estão utilizando bombas de vácuo de palhetas, com consumo zero de água, mas com contato entre as palhetas e a parte interna da carcaça do rotor, o que vai gerar a necessidade maior de manutenção.”
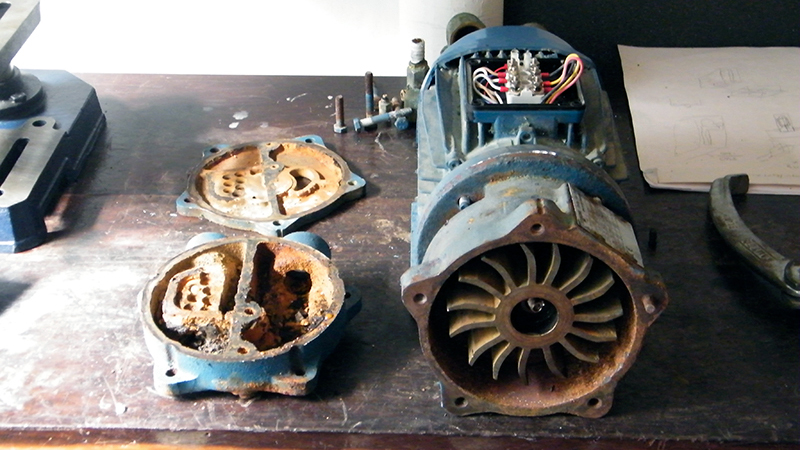
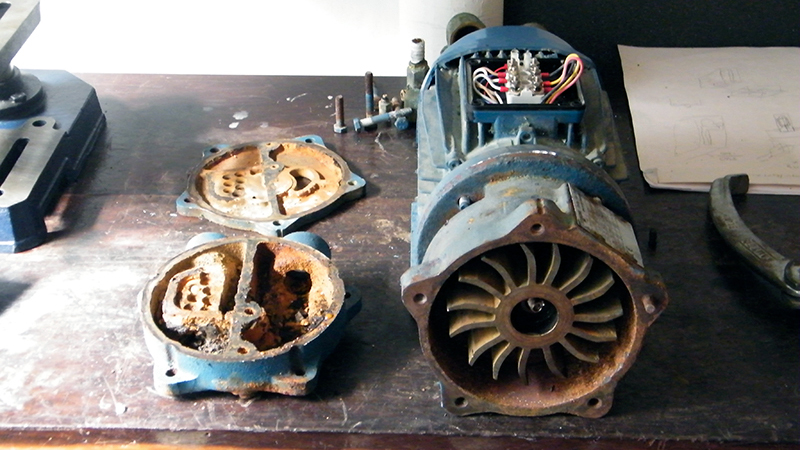
21.3 guarnição da autoclave
Responsável pela vedação da câmara de esterilização, é um componente que danificado impede o funcionamento da autoclave. Podem ser fixas, mas na grande maioria das autoclaves produzidas atualmente, são posicionadas em uma canaleta e se movimentam, em direção a porta para a vedação da câmara de esterilização ou recolhendo para o interior da canaleta para permitir a abertura da porta. Algumas guarnições necessitam de lubrificação periódica onde são utilizadas graxas especiais, grafite ou lubrificantes secos como bissulfeto de molibdênio. Alguns fabricantes de autoclaves tratam a superfície interna das canaletas de maneira que a lubrificação se torna desnecessária aumentando a vida útil da guarnição. Em relação a sua vida útil vai depender do fluido usado para a sua pressurização, se é o vapor ou ar comprimido, do número de ciclos realizados durante o dia, do intervalo entre lubrificação (quando for o caso). Da experiência de serviços realizados em autoclaves com contrato de manutenção, a vida útil de uma guarnição varia de 6 a 10 meses.
21.4 placa de controle
Atualmente é muito raro encontrar autoclaves com controladores que não sejam um CLP. Controlador Lógico Programável, e este controlados, além do CPU onde está toda a programação do equipamentos possui mais componentes como o cartão de entrada analógica responsável pela entrada dos sensores de temperatura e pressão, o cartão de entrada digital que é o responsável por informar o CPU de condições durante o processo como a situação da porta (aberta ou fechada), da situação da câmara (vedada ou não), da bomba de vácuo (ligada ou desligada) e todas as outras necessárias para o funcionamento do equipamento. Tem ainda o cartão de saída digital que controla o acionamento dos componentes da autoclave, como abertura e fechamento de válvulas, ligar ou desligar motores, abrir ou fechar as portas e todos os outros componentes que necessitam ser acionados ou desacionados na autoclave. A robustez das placas de controle ou os cartões eletrônicos varia de fabricante para fabricante, mas alguns cuidados são importantes para a sua durabilidade. Primeiro temos que considerar o ambiente da instalação do controlador. Conheço algumas instalações onde a temperatura e umidade na área técnica atingem valores que ajudam a diminuir a vida útil das placas, a qualidade da energia elétrica também tem grande influência, principalmente com interrupções de fornecimento (vale a pena analisar a necessidade da instalação de um nobreak com estabilização para a alimentação elétrica do controlador) e lógico os cuidados com a operação.
“Conheço algumas instalações onde a temperatura e umidade na área técnica atingem valores que ajudam a diminuir a vida útil das placas, a qualidade da energia elétrica também tem grande influência, principalmente com interrupções de fornecimento (vale a pena analisar a necessidade da instalação de um nobreak com estabilização para a alimentação elétrica do controlador) e lógico os cuidados com a operação.”
Muitas vezes o primeiro componente do controlador que sofre danos é o IHM (interface homem máquina), aquela tela com teclados que permite a abertura das portas e iniciar ciclo e que fornece informações gravadas e em tempo real para o operador acompanhar o processo. Faço manutenção em equipamentos com mais de 15 anos no qual nenhum componente do CLP foi substituído, mas também conheço equipamentos que em 15 anos o CLP foi totalmente substituído por danos em suas peças durante este período.
21.5 trocador de calor
Alguns equipamentos trabalham com trocadores de calor para várias funções, como para descartar condensados em temperaturas aceitáveis para o sistema de drenagem da instalação predial, para reaproveitamento da água utilizada na bomba de vácuo ou ainda aquele instalado logo após a válvula do dreno da autoclave que ajuda muito da realização do vácuo, principalmente após a fase de esterilização. Isto porque 1 litro de água ocupa mais de 880 litros na forma de vapor saturado em ciclos de 121 °C e mais de 600 litros em ciclos de 134 °C. Quando o vapor passa pelo trocador de calor ele condensa e seu volume diminui em 880 vezes para os ciclos de 121 °C ou 600 vezes para os ciclos de 134 °C. Esta redução de volume gera um vácuo no trocador de calore com isto melhora a capacidade da realização do vácuo na câmara de esterilização. Trocadores de calor tem vida útil longa e depende principalmente do material que é construído e dos contaminantes do vapor de alimentação da autoclave. ♦
Tales Brito
Formado em engenharia mecânica em 1986 pela Escola Federal de Engenharia de Itajubá, atua na área de esterilização e desinfecção desde 1995. A partir de 1998, como sócio/diretor da empresa Pharma Ltda e com treinamentos voltados para instalação e comissionamento nas empresas Getinge (Suécia), Lytzen (Dinamarca), Lancer (França) e Erweka (Alemanha), vem atuando juntamente com o representante dessas no Brasil, na instalação, comissionamento, treinamento operacional, treinamento de manutenção e manutenção em mais de 150 equipamentos voltados para a limpeza, desinfecção, esterilização e controle de qualidade em hospitais e indústria farmacêutica. Desde 2010, atua também como gerente técnico do laboratório de calibração da Pharma Ltda. A empresa atua no mercado desde 1998 e nasceu com o objetivo de realizar manutenção em equipamentos médico-hospitalares. A partir deste objetivo, se especializou na área de desinfecção e esterilização. Contratada como autorizada técnica pelos representantes da Getinge no Brasil, passou a atuar na instalação, validação, treinamento de operação e manutenção e, assistência técnica para lavadoras termodesinfectoras e autoclaves à vapor saturado. Aproveitando a experiência acumulada e atendendo às necessidades do mercado, em 2009, a Pharma Ltda disponibilizou seu Laboratório de Calibração. Como reconhecimento da qualidade da calibração, o laboratório da Pharma Ltda foi acreditado pela Coordenação Geral de Acreditação do Inmetro (CGCRE) em 2010, segundo os requisitos estabelecidos na ABNT NBR ISO/IEC 17025 para serviços nas grandezas Temperatura e Pressão, para calibração no próprio laboratório ou nas dependências do cliente. Hoje a Pharma Ltda é uma empresa consolidada no mercado e conta com equipamentos de alta tecnologia e uma equipe de profissionais altamente qualificados para garantir a confiabilidade e a credibilidade dos serviços prestados.
Jornalista responsável: Stella Curzio – MTB 70289/SP